Summary:Oil type mold temperature control machine is designed to regulate the temperatures of plastic parts....
Oil type mold temperature control machine is designed to regulate the temperatures of plastic parts. The heat transfer between the oil and the heat medium is dependent on the wall thickness, so it is important to choose the temperature that will prevent pyrolysis from taking place. If the temperature is too high, the plastic part may not be finished as desired. An oil type mold temperature control machine should be set at a maximum of 200 degrees C and must be calibrated periodically.
This machine uses a water-based heating media for heat exchange. Its standard temperature control is 200 degrees Celsius, while its high-temperature control is 300 degrees. The wide temperature range and excellent heat stability are important factors in selecting the oil-type mold temperature control machine. The heating and cooling process is simple and requires only a few components, such as thermostats and thermometers. The pumping process takes a few minutes, and the mold temperature controller is equipped with all the necessary tools and controls.
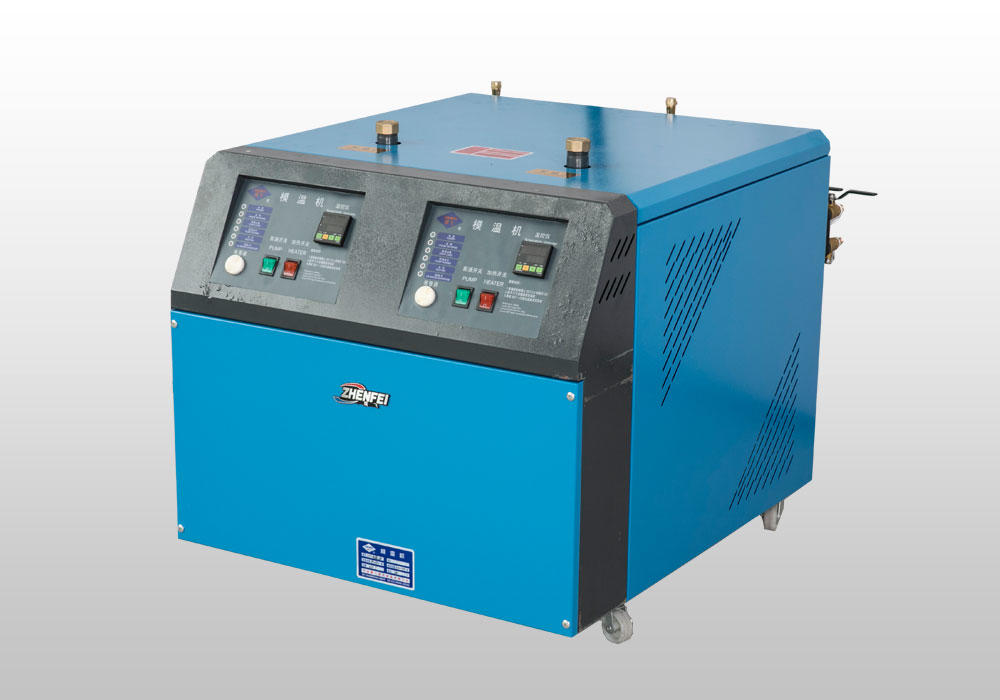
The mold temperature control machine is equipped with additional controls and buttons to help users manage the temperature. If there's a fault with the machine, the process may fail. The system is either not regulated enough or the temperature sensors are defective. If the controller is not operating properly, the fluid in the tank is low, causing the temperature to rise and the process to fail. The device should have a means to correct these problems, as well as a method to refill the fluid.
Oil type mold temperature control machine comes with extra buttons and controls. The operator needs to be highly trained to operate the machine. He or she should have proper knowledge of the various parts of the machine. The Control Unit is the most important component of the machine as it has all the necessary controls. The device should also have a range of temperature settings and will allow the user to choose the desired parameters. The best thing to do is to choose the appropriate machine for the industry.
The mold temperature control machine should be suitable for the production of plastic products. The machine must be compatible with different types of thermometers. The machine must have a cooling system that can be set to a temperature above 100 degC. It should also have additional buttons that allow users to adjust the temperatures. The device must also have a cooling system that can be turned off and on at will. A malfunctioning oil type mold temperature control machine can lead to a failure in the process.
An
oil type mold temperature control machine is important for the production of plastic products. It is important for the machine to be able to reach the desired temperature range. It should also have good thermal conductivity. It should have a range of temperatures that will not be dangerous to the product. When the maximum temperature of the plastic is over 300°C, it should be in closed working mode to avoid evaporation. It should also be equipped with a pump.
The oil type mold temperature control machine should have a cooling system that can supply the required amount of water. Ideally, the cooling system should have two cooling channels: one for the plastic and one for the oil. A water-based solution can be used for cooling the oil-type molds. It is best to use a fluid-free machine for the production of plastic parts. However, if the cooling system has a pressure sensor, then it is not sufficient.
An oil type mold temperature control machine is designed to control the temperature of plastic parts. It is a great option for manufacturing plastic products. The machine uses water as its heating medium and is able to achieve heat exchange by indirect cooling. The machine has a range of 200 degrees and high temperature control up to 300 degrees. The control range of this machine is very wide and the heat stability is excellent. Its self-pressure-releasing system allows it to be adjusted without having to stop the production process.